D-shape Blind Nuts, also known as D-shaped clinch nuts or D-ring Blind Nuts, are specialized Fasteners designed for applications where access to the nut's opposite side is restricted. These nuts feature a D-shaped cross-section, allowing them to be installed in thin materials like sheet metal using a clinching or press-fit process. This article explores the materials used in D-shape Blind Nuts and the manufacturing processes involved in their production.
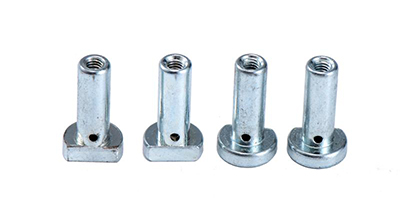
Materials Used in D-shape Blind Nuts
D-shape blind nuts are typically made from high-strength, corrosion-resistant materials to ensure durability and reliability in various environments. The most common materials include:
Aluminum: Aluminum D-shape blind nuts are lightweight and offer good corrosion resistance. They are often used in automotive, aerospace, and electronic applications where weight reduction is crucial.
Steel: Steel nuts provide high strength and durability. They are suitable for heavy-duty applications where high tensile forces are expected. Stainless steel variants offer enhanced corrosion resistance, making them ideal for outdoor or marine environments.
Brass and Bronze: These materials are used for applications requiring good electrical conductivity and corrosion resistance. Brass and bronze nuts are often found in electrical connectors and decorative hardware.
Plastic: In some applications, plastic D-shape blind nuts are used to reduce weight and cost. They are typically made from nylon, polycarbonate, or other engineering plastics that offer good mechanical properties and chemical resistance.
Manufacturing Processes
The manufacturing of D-shape blind nuts involves several steps, from raw material preparation to final assembly and testing. Here's a detailed look at the processes involved:
Material Preparation: The raw material, whether it's aluminum, steel, brass, or plastic, is first cut to the required length and diameter. For metallic materials, this may involve cold drawing or hot rolling processes to achieve the desired shape and size.
Forming: The raw material is then formed into the D-shape cross-section. This is typically done using a stamping or forging process. In stamping, a punch presses the material into the desired shape, while forging involves hammering or pressing the material to shape it.
Threading: The internal threads of the nut are created using a threading process, such as rolling, cutting, or tapping. Rolling threads is a popular method because it creates stronger, more durable threads than cutting or tapping.
Surface Treatment: To enhance corrosion resistance and aesthetic appeal, D-shape blind nuts may undergo surface treatment processes such as plating, painting, or anodizing. Plating involves depositing a thin layer of metal (e.g., zinc, chromium) onto the surface, while painting and anodizing provide protective coatings through chemical reactions.
Inspection and Testing: Finally, each nut is inspected for defects and tested to ensure it meets the required specifications. This may include checking thread pitch, diameter, and material thickness, as well as performing tensile strength and corrosion resistance tests.
Installation and Application
D-shape blind nuts are installed using a special tool called a clinching tool or press-fit tool. This tool pushes the nut into a pre-drilled hole in the workpiece, causing the D-shaped flanges to spread and lock into place. The resulting installation is secure and vibration-resistant, making D-shape blind nuts ideal for applications where reliability and strength are critical.
D-shape blind nuts are versatile fasteners that offer a range of benefits, including ease of installation, high strength, and corrosion resistance. Their manufacture involves careful selection of materials and precision manufacturing processes to ensure they meet the rigorous standards of various industries. By understanding the materials and manufacturing processes involved, engineers and designers can specify D-shape blind nuts confidently for their applications.