Blind Rivets, commonly known as pop rivets, have become an essential fastening solution in the automotive industry. Their unique ability to provide strong, permanent connections from one side of a material makes them ideal for various automotive applications. This article explores the critical role of Blind Rivets in assembling vehicle components, highlighting their benefits, applications, and the reasons for their growing popularity in automotive manufacturing.
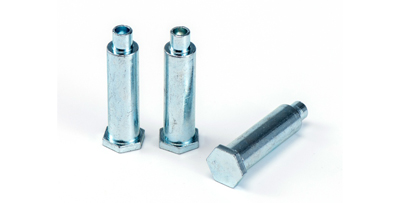
The Importance of Blind Rivets
In the automotive sector, weight reduction and structural integrity are paramount. Blind rivets offer a lightweight yet robust fastening method that contributes to these goals. They provide excellent shear and tensile strength, ensuring that components remain securely attached, even under the demanding conditions of vehicle operation.
Key Applications of Blind Rivets in Automotive Manufacturing
Body Panel Assembly:
Blind rivets are extensively used to attach body panels, such as doors, hoods, and fenders. Their one-sided installation feature allows for efficient assembly, especially in areas where access is limited. This reduces labor costs and assembly time, making the manufacturing process more efficient.
Chassis and Frame Construction:
Interior Components:
Blind rivets are also utilized in assembling interior components, such as dashboards, seats, and trim pieces. Their aesthetic appeal is a significant advantage, as they can create a clean and finished look without visible Fasteners.
Electrical and Wiring Harnesses:
Exhaust Systems:
Advantages of Using Blind Rivets in Automotive Manufacturing
Efficiency: The one-sided installation feature of blind rivets allows for quicker assembly processes, reducing labor time and costs. This efficiency is critical in high-volume production environments.
Weight Reduction: Blind rivets are lightweight compared to traditional fasteners like Bolts and nuts. This contributes to the overall weight reduction of vehicles, enhancing fuel efficiency and performance.
Versatility: Available in various sizes, materials, and head styles, blind rivets can be used in diverse applications, making them a versatile choice for automotive manufacturers.
Cost-Effectiveness: The reduced assembly time and lower material costs associated with blind rivets contribute to overall cost savings in the manufacturing process.
Strength and Durability: Blind rivets provide strong, permanent connections that can withstand significant forces, ensuring the longevity and reliability of vehicle components.
Blind rivets play a vital role in automotive manufacturing, offering a combination of strength, efficiency, and aesthetic appeal. Their ability to provide secure connections in various applications—from body panels to chassis construction—makes them indispensable in the automotive industry. As manufacturers continue to seek ways to optimize production processes and improve vehicle performance, the use of blind rivets is likely to expand, solidifying their place as a preferred fastening solution in automotive design and assembly.