Hexagon Head Screws are essential Fasteners used in a wide variety of industries, including automotive, construction, machinery, and electronics. Known for their durability and strength, these Screws are designed to withstand significant mechanical stress and provide reliable fastening solutions. The manufacturing process of hexagon head Screws is intricate, involving multiple stages—from the initial design phase to the final quality control tests. In this article, we will provide a detailed look at the manufacturing process of hexagon head screws, focusing on each step involved in their production.
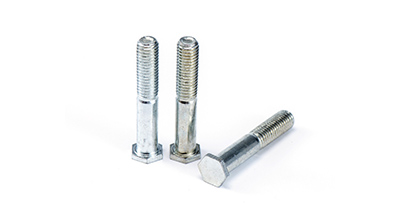
1. Raw Material Selection
The manufacturing process begins with the selection of raw materials. The choice of material is crucial for determining the strength, corrosion resistance, and overall durability of the finished hexagon head screws.
Common Materials for Hexagon Head Screws:
Carbon Steel: The most commonly used material for general-purpose screws. It offers excellent strength and is cost-effective.
Stainless Steel: Used when corrosion resistance is important, particularly in industries like food processing, marine, and pharmaceuticals.
Alloy Steel: Provides high strength, making it ideal for applications that require resistance to high pressures and extreme conditions.
Brass or Copper: Used in specific applications where electrical conductivity or corrosion resistance is essential.
Once the material is selected, it is sourced in the form of wire rods or bar stock, which are then processed into screw blanks during the initial stages of manufacturing.
2. Wire Drawing and Cold Heading
The raw material, typically in the form of wire, is drawn into the appropriate diameter size before being fed into a cold heading machine. Cold heading is a process where the metal wire is shaped into the preliminary form of the screw head by applying high pressure.
Cold Heading Process:
Forming the Head: The wire is cut into short lengths, and each piece is placed in a die. The die then presses the wire to form the basic shape of the hexagon head. This is done at room temperature, which allows the metal to retain its structural integrity.
Shaping the Threads: In some cases, after the head is formed, the threaded portion of the screw is also shaped using a cold forming technique, which helps create strong, precise threads that will later engage securely with a nut or another screw.
The cold heading process is essential for producing the screw head, which will later be machined to the precise hexagon shape needed for efficient tightening.
3. Machining and Thread Rolling
After the initial cold heading, the screw blank is sent to machining stations for further shaping and precision work.
Hexagon Head Machining:
Thread Rolling:
Thread rolling is a key process for shaping the threads of the screw. This process is done by rolling the screw blanks between two rotating dies with precise thread patterns.
Cold Rolling: In thread rolling, the material is not removed, but rather the threads are formed by displacing the metal. This process is faster and more cost-effective than traditional cutting methods, and it produces stronger threads by aligning the material's grain structure.
Benefits of Thread Rolling: Thread rolling creates stronger, more durable threads with improved resistance to wear and tear. Additionally, this method produces smoother threads, which helps ensure a better fit between the screw and the mating material.
4. Heat Treatment
After the threads are formed, the screws undergo heat treatment to further improve their mechanical properties. Heat treatment involves heating the screws to a specific temperature and then cooling them rapidly.
Heat Treatment Process:
Hardening: The screws are heated to a high temperature and then quenched in oil or water. This process increases the hardness of the screw, making it more resistant to wear and deformation.
Tempering: To reduce the brittleness of the hardened screw, tempering is performed. The screws are reheated to a lower temperature and then cooled slowly to achieve the desired balance between hardness and toughness.
Heat treatment is crucial in determining the final strength and durability of the screw, ensuring that it can withstand the mechanical stresses encountered during use.
5. Surface Finishing and Coating
Once the screws have been heat-treated, they undergo a surface finishing process. This stage ensures that the screws not only perform well but also have an appealing appearance and resist corrosion.
Surface Finishing Options:
Plating: Common surface treatments for hexagon head screws include zinc plating, chrome plating, and nickel plating. These finishes provide corrosion resistance, improve the aesthetic appeal, and increase the longevity of the screws.
Black Oxide Coating: This finish adds a layer of protection against corrosion while providing a sleek, matte finish.
Anodizing: For screws made of aluminum or other non-ferrous metals, anodizing is used to increase corrosion resistance and wear resistance by creating a protective oxide layer on the surface.
Oil Coating: Sometimes, a thin layer of oil is applied to prevent rust during storage and transport.
Surface treatments not only enhance the screw's performance but also improve its visual appeal, especially for screws used in visible or consumer-facing applications.
6. Quality Control and Inspection
Before the hexagon head screws are packaged and shipped, they go through a final inspection process to ensure that they meet the required quality standards.
Key Quality Control Checks:
Dimensional Inspection: Every screw is checked to ensure it meets the correct dimensions for head size, thread pitch, and length. Automated measuring machines are used to perform precise measurements.
Strength Testing: Tensile and shear tests are conducted to ensure that the screws can withstand the forces they will experience during use.
Surface Inspection: The screws are examined for defects such as cracks, chips, or irregularities in the plating.
Torque Testing: The screws are tightened to a predetermined torque value to ensure that they can handle the expected load without failure.
Only screws that pass these tests are approved for shipment to customers.
7. Packaging and Distribution
Once the screws pass quality control, they are packaged in bulk or in smaller quantities, depending on customer specifications. Proper packaging is essential to prevent damage during transit and to ensure that the screws remain in optimal condition. The packaged screws are then shipped to distributors or directly to end users.
The manufacturing process of hexagon head screws involves several critical stages—from raw material selection and cold heading to threading, heat treatment, surface finishing, and quality control. Each step is essential to ensure the screws are durable, reliable, and meet industry standards for strength and performance. By understanding the detailed steps involved in the manufacturing process, manufacturers can produce high-quality hexagon head screws that meet the specific needs of their customers, whether they are used in automotive, industrial, or construction applications.