D-Profile Dowel Pins are essential components used across a wide range of industrial applications, providing secure, stable alignment in machinery and mechanical assemblies. These specially designed pins, with their flat side, offer superior holding power compared to traditional round dowel pins, preventing unwanted rotation in applications requiring precise positioning. The process of creating high-quality D-Profile Dowel Pins involves several key stages, including material selection, precision machining, surface treatment, and stringent quality control measures. Let’s examine each of these steps in detail.
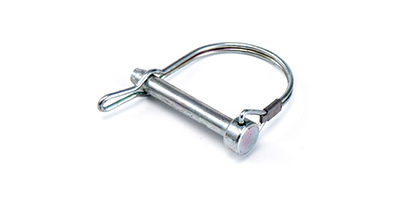
The first step in the manufacturing process is selecting the right material for the pins. The choice of material impacts the performance, durability, and overall functionality of the dowel pins. The materials commonly used for D-Profile Dowel Pins include:
Carbon Steel: Offers good strength and hardness, making it ideal for general applications where wear resistance is needed.
Stainless Steel: Known for its resistance to corrosion, stainless steel is preferred in environments that involve exposure to moisture or chemicals.
Alloy Steel: Often used in high-stress applications, alloy steel provides excellent strength and wear resistance.
Bronze and Brass: These materials are selected for their excellent corrosion resistance and are commonly used in more specialized applications.
Choosing the appropriate material depends on the specific demands of the application, including factors such as load capacity, environmental conditions, and wear resistance.
2. Precision Machining
Once the material is selected, the next crucial step in manufacturing D-Profile Dowel Pins is precision machining. This involves shaping the material to the required dimensions while ensuring accuracy and uniformity across each pin.
Cutting and Shaping: The raw material is initially cut into the desired length and diameter. The pin is then machined to create the distinct D-profile, which involves flattening one side of the pin while ensuring the remaining round portion is maintained to exact specifications. This step requires high precision to ensure the flat side is perfectly aligned, as this flat section is what prevents rotation in mechanical assemblies.
Turning and Grinding: After the basic shape is created, the pins are further refined through turning and grinding processes to achieve the required tolerances and surface finish. These processes ensure that the pins are smooth, uniform, and free from any defects that could affect their performance.
Drilling and Holes (if applicable): Some D-Profile Dowel Pins are designed with holes for securing them in place with a cotter pin or other Fasteners. If required, this additional step is carried out with high precision.
3. Surface Treatment
To enhance the durability, corrosion resistance, and aesthetic appeal of D-Profile Dowel Pins, surface treatment processes are employed. The treatment chosen depends on the material and the intended application:
Zinc Plating: A common choice for steel and alloy pins, zinc plating provides a protective layer against corrosion, extending the pin's lifespan, especially in humid or outdoor environments.
Black Oxide Coating: This treatment creates a thin, rust-resistant layer that improves wear resistance and provides a sleek, black finish. It is often used for steel pins exposed to less extreme conditions.
Nickel Plating: For applications that require superior corrosion resistance, nickel plating is often applied, particularly on stainless steel or alloy steel pins.
Phosphating: This treatment creates a protective, non-reflective surface and enhances the pin's ability to withstand wear and tear, making it ideal for heavy-duty applications.
4. Quality Control Measures
Given the critical role that D-Profile Dowel Pins play in machinery and mechanical systems, strict quality control (QC) measures are employed throughout the manufacturing process. This ensures that the pins meet the necessary standards for strength, precision, and performance.
Dimensional Inspection: Every batch of pins undergoes a rigorous dimensional check to ensure that the D-profile is accurately formed. High-precision measuring tools, such as micrometers and calipers, are used to confirm the diameter, length, and flatness of the pins.
Tensile Testing: To ensure the pins can handle the required load without deformation or failure, tensile strength tests are performed. These tests measure how much force the pin can withstand before breaking or bending, ensuring the pins meet strength specifications.
Surface Finish Inspection: The surface quality is checked for defects such as cracks, pits, or imperfections that could affect the pin’s performance. A smooth, consistent surface is critical to the pin's ability to align and fit securely within mechanical systems.
Corrosion Testing: For pins made from materials that require corrosion resistance, salt-spray tests or accelerated aging tests are conducted to simulate prolonged exposure to harsh environments and ensure the protective coatings are effective.
Batch Testing: Random sampling from each production batch undergoes extensive testing to ensure uniform quality across all units. This step ensures that every batch of pins performs consistently, meeting both customer requirements and industry standards.
The manufacturing of D-Profile Dowel Pins is a highly precise and intricate process that combines material selection, advanced machining, surface treatment, and rigorous quality control measures. The result is a reliable, durable, and high-performance component used in a wide array of industrial applications, from machinery and automotive systems to construction equipment and aerospace technology. By ensuring the pins meet stringent standards of strength, accuracy, and corrosion resistance, manufacturers are able to provide a product that guarantees optimal performance and longevity, even in the most demanding environments.