Phillips self-drilling Screws are essential Fasteners used in a variety of applications, from construction to automotive and electronics. These Screws combine the functionality of drilling and fastening into a single step, eliminating the need for pre-drilled holes and offering an efficient solution for many fastening tasks. However, to ensure optimal performance and long-lasting results, it's important to follow some key installation tips when using Phillips self-drilling Screws. In this article, we will discuss the essential tips for properly installing Phillips self-drilling screws.
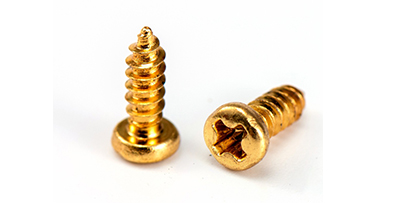
1. Ensure Proper Alignment to Prevent Misalignment and Bending
One of the most critical aspects of installing Phillips self-drilling screws is ensuring that the screw is aligned properly with the surface of the material. Misalignment can lead to several issues, including bent screws, stripped heads, and poor thread engagement. To avoid these problems:
Hold the screw perpendicular to the surface to ensure it enters the material at the correct angle.
Use a drill with a level or a guide tool to maintain accurate alignment during installation, especially when working with larger screws or in tight spaces.
Proper alignment ensures that the screw penetrates the material straight, which improves its holding power and reduces the likelihood of damaging the material or the screw.
2. Use the Correct Drill Speed
Choosing the right drill speed is crucial when installing Phillips self-drilling screws, as the speed directly impacts the drilling efficiency and screw performance.
Too fast a drill speed can lead to overheating of the screw, which may cause the material to crack or the screw to become damaged.
Too slow a speed can result in an ineffective drilling process, reducing the screw's ability to drill through tougher materials and making installation more time-consuming.
The ideal speed will depend on the material you're working with, but generally, moderate drill speeds work best for most applications. If the screw is not going in easily, slightly increasing the speed may help. However, it's important to avoid excessive speed to prevent damaging the screw or the material.
3. Pre-Tap if Necessary for Hard Materials
In some cases, especially when working with very hard or dense materials like thick metals or composites, you may need to pre-tap a small hole before installing the screw. Pre-tapping can help the screw to engage more easily, reducing the stress on both the screw and the material.
Pre-tapping a hole creates a pilot hole that guides the screw, making it easier for the self-drilling tip to penetrate the material. This is particularly useful when drilling into stainless steel, aluminum, or other tough metals.
For softer materials like wood or plastic, pre-tapping is usually not necessary, as the self-drilling screw is more than capable of creating its own hole.
To pre-tap, use a drill bit slightly smaller than the screw’s outer diameter. After the hole is created, insert the Phillips self-drilling screw as usual.
4. Choose the Correct Phillips Bit
Using the correct Phillips bit is essential to the success of the installation. The Phillips drive system is designed to provide maximum torque transfer, but to ensure this happens effectively, the bit must fit snugly into the screw head.
Avoid using worn or damaged Phillips bits, as these can cause the screw to slip and strip, leading to poor performance or failure.
Ensure the bit size matches the screw size. Using a too-small bit can result in insufficient torque transfer, while a too-large bit can cause the screw to slip or become misaligned.
Always select a high-quality Phillips bit that is designed specifically for the type of screw you're using. If you're working with a larger screw or in a high-torque application, consider using an impact driver bit for added performance.
The right bit ensures that the torque is applied efficiently, preventing cam-out (when the bit slips out of the screw head) and ensuring smooth and secure fastening.
5. Apply Consistent Pressure During Installation
While installing Phillips self-drilling screws, it is important to apply consistent and even pressure. This ensures that the screw moves smoothly into the material without becoming misaligned or encountering resistance that could lead to damage.
Apply steady, even pressure to the drill or screwdriver, and allow the screw to drill itself in rather than forcing it.
Too much pressure can lead to over-tightening, which may cause the screw to break, strip, or cause material deformation.
If the screw begins to slow down or feel resistant, pause briefly to check if the drill speed or alignment needs adjusting before continuing.
By applying consistent pressure, you ensure that the screw performs at its best and remains securely fastened.
6. Avoid Over-Tightening the Screws
While it may seem tempting to tighten screws as much as possible to secure the material, over-tightening can actually cause more harm than good. Over-tightening can:
Lead to stripped screw heads.
Crack or deform the material you are fastening.
Cause stress fractures in the screw itself, leading to premature failure.
The best practice is to tighten the screw until it feels securely seated, and then stop. If you are unsure, test the screw's holding strength by gently trying to pull the material apart. It should hold firmly without any risk of loosening.
7. Use the Right Screw for the Material
Phillips self-drilling screws come in various sizes, lengths, and coatings to suit different materials and applications. Always select the appropriate screw for the material you're working with. For example:
For metal: Use screws that are specifically designed for metal applications, with hardened steel or corrosion-resistant coatings like zinc or black oxide.
For wood: Choose screws with a thread design optimized for wood, which will ensure better grip and minimize damage to the material.
For outdoor use: Consider stainless steel screws to provide enhanced corrosion resistance in humid or outdoor environments.
Using the correct screw ensures a tight, secure fit and reduces the likelihood of installation issues down the line.
8. Regularly Inspect and Replace Damaged or Worn Screws
During installation, always inspect the screws to ensure that they are in good condition. Using a damaged or worn screw can lead to installation failures, poor performance, or weakened fastenings.
Look for any bent, stripped, or corroded screws before use. If the screw has visible damage, replace it with a new one.
Check the threads for any signs of wear, as worn threads can make it difficult for the screw to grip the material effectively.
Replacing damaged screws before installation prevents frustration and ensures a more reliable and secure connection.
Installing Phillips self-drilling screws correctly is essential to ensure that your fasteners perform at their best. By following these key installation tips—ensuring proper alignment, using the correct drill speed, pre-tapping when necessary, choosing the right bit, applying consistent pressure, and avoiding over-tightening—you can significantly improve the quality and durability of your installations. Phillips self-drilling screws offer many advantages, including faster installation and eliminating the need for pre-drilled holes, but proper technique is vital to unlocking their full potential.